
|
 |
 |
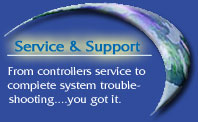
The Nordiko
2000 Sputtering System offers the highest degree of process flexibility in
the industry. The Nordiko 2000 systems are batch type annular geometry's
with modular options allowing a wide range of operating parameters and
configurations |

The
chamber lid or baseplate can accommodate up to four (4) 8" diameter (six (6) 8"
or four (4) 10" diameter in 8550) sputtering cathodes for either up or down
deposition. Sputter-up is recommended for system cleanliness and particle control.
Sputter-down is beneficial for hard to fixture irregular substrates and for edge coverage
requirements. |
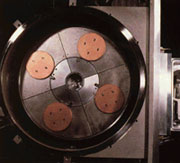
All segments may be configured
identically, for a dedicated process yielding higher substrate throughputs. A dedicated
substrate holder may also be provided in lieu of a segmented type to further increase the
load sizes for pilot/production applicability.
For further process flexibility the entire
substrate table may be raised or lowered through a range of 4" (l00mm), even in
mid-process. This allows for optimization of deposition rate versus uniformity to be
undertaken with ease. Additionally, thick or 3-dimensional substrates may be accommodated
without system modification.
|
|
 |
 |
|
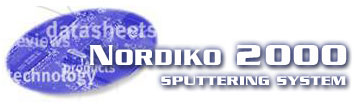
The Nordiko 2000 is designed
primarily for R&D (Advanced Process Development) and Pilot
Production applications. The "base" Nordiko 2000 can be
configured without an automation system or load lock for
restricted budgets. These items can be modularly added on as
the application and funds develop. |
|
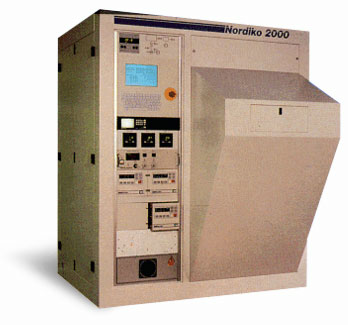 |
- 24.5" (600mm) diameter stainless
steel substrate table.
- Up or down sputtering
geometry's.
- Four sputtering electrodes; 2",
3", 4", 6", and 8" diameter (50mm, 75mm, 1 00mm, 1 50mm, and
200mm diameter) planar target electrodes.
- Sequential or co-deposition
sputtering modes.
- Target electrodes are arranged
in the same plane as standard, but cluster-focused or off-axis
geometry's are available
- Source to substrate distance may
be varied during process.
- Work holder may be dedicated to
a full load of wafers, or segmented to allow for a variety of
process options.
- Work holder may be used in
static or rotational operation.
- Substrate heat to 350ºC, 550ºC
or 850ºC.
- Substrate cooling via
water-cooled or gas injected work holder with auto clamping.
- High power RF bias with
excellent power transfer stability during rotation.
- RF etch capability.
- Ion Beam "soft etch" using
Nordiko's patented RF excited filamentless ion beam gun.
- Automated load lock (optional on
2000).
- Process control automation
system (optional on 2000).
- AII mechanized set-points are
stored in software for easy adjustment from key board
(optional on 2000).
- Installation through clean room
wall or free standing.
- All servicing from rear of
machine.
- Small foot print.
|
Control of pumpdown, valving,
wafer transfer, and deposition is provided by a Model 5TI
Process Controller. This Controller is simple, reliable, and
also has a manual control feature to facilitate maintenance and
enable the performance of special processes requiring manual
control.
|
|
|
|
|