
|
 |
 |
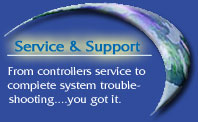
Sputter
up and sputter down modes are easily chosen and keep particulate
contamination of the substrate to a minimum by sputtering up, odd shape
and irregular substrates can be processed in sputter down mode. |
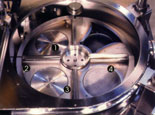
The CVC 611
can process substrates on pallets or directly and up to
six substrate pallets can be processed per run. Cassette in
cassette substrate processing is possible for most substrates. |
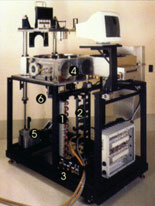
The CVC 611 is built with open architecture
and by removing
the dress covers, the entire mechanical and electric subsystems
become accessible for service and maintenance.
The CVC
611 LOADLOK sputtering system can process substrate pallets
one at a time through the optional robotic chamber slit valve. |
|
 |
 |
|

The CVC
LOADLOK system has been designed with maximum thin film
sputtering process flexibility as major objective....for
the research and development scientist or production process
engineer, the CVC 611 is an ideal tool for dependable cost effective
operation.
Eight work stations accept combinations of RF magnetron, RF
diode, DC magnetron planar sputtering cathodes . . . Up to eight
materials may be deposited, with sequential or co-sputter deposition. |
|
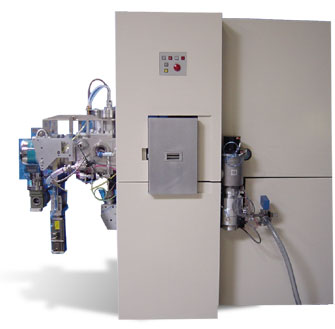 |
Product
throughput of the CVC 611 LOADLOK is ideal for many production
applications. For pilot production the CVC 611 is unsurpassed.
Use the same system for process development and production.
The CVC
ICS 660 ION CLEANING source can be installed in any work
station. The 7.5 inch diameter low energy ion beam, designed
for substrate preclean is today's alternative to sputter etch.
It ensures minimized particulate generation, creates smoother,
uniform surfaces, and causes less substrate damage.
|
Automated
process control with real-time processing . . . A Techware PAL-68000
real-time process controller provides overall One button"
control. Full screen color graphics, three levels of programming,
20 MB hard drive, data logging, seven levels of passwords, self-diagnostics
and modem support are some of the features on the CVC 611.
Quick
Change Targets QCT are used on all work stations,
therefore, changing sputtering targets can be done quickly, with minimum
system down-time.Titanium
shielding and substrate holders . . . Titanium is dimensionally
stable, light weight for easy and safe handling and will with
stand rigorous cleaning regimens.
The CVC
ROTOSTRATE . . . This concept of rotating the substrate
over the targets ensures excellent film uniformity, repeatability,
and allows for true co-deposition.
The CVC 611 can be mounted in a clean room through-the-wall
or free standing.
|
|
|
|
|